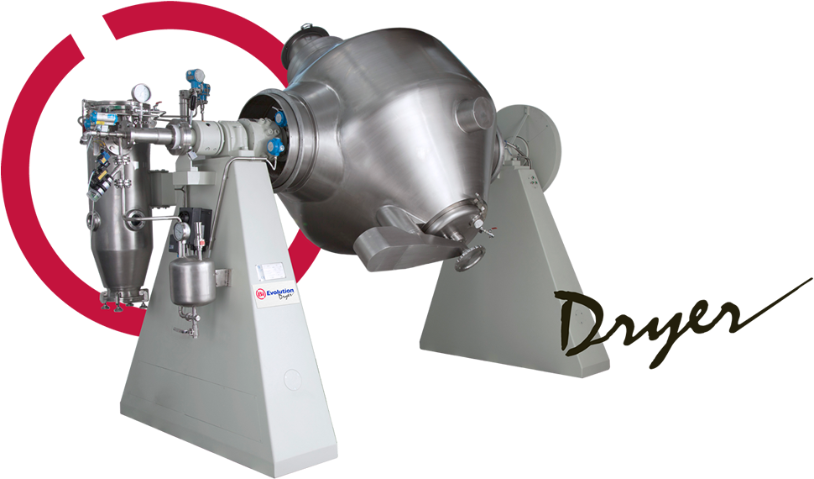
A shape designed for the best possible results
Everything in Bi-Evolution Dryer®, from the robust structure to the smallest detail, is conceived to grant the best possible effectiveness of the drying process. The central body of Bi-Evolution Dryer® consists of a bi-conical rotating drying chamber, characterized by soft lines without edges and sharp corners.
During the rotation, this dryer allows the total and continuous revolution of the product mass to be dried and homogenously mixed. The speed of rotation of the chamber is adjustable, permitting an agitation ranging from delicate to moderate.
This allows even the processing of products with weak bonds, without modifying their molecular structure. Regarding the parts in contact with the product, the standard version of Bi-Evolution Dryer® is made of stainless steel 316L, but on request it can be made of other weldable materials, such as Hastelloy C-22 and stainless steel type 904L or coated.
Effective filtering systems on the inner suction pipe
The filtering unit must be able to keep all of the powder in the drying chamber, letting only the solvent vapours pass through. At the same time, it must ensure the lowest possible pressure drop, in order to achieve very low final pressure values. Italvacuum offers filtering systems able to meet all of the process requirements: i.e. metal sintered cartridge filters or PTFE filters, suitable for very small diameter powders and whose effectiveness during the process is ensured by an automatic cleaning system for nitrogen back-flow washing.
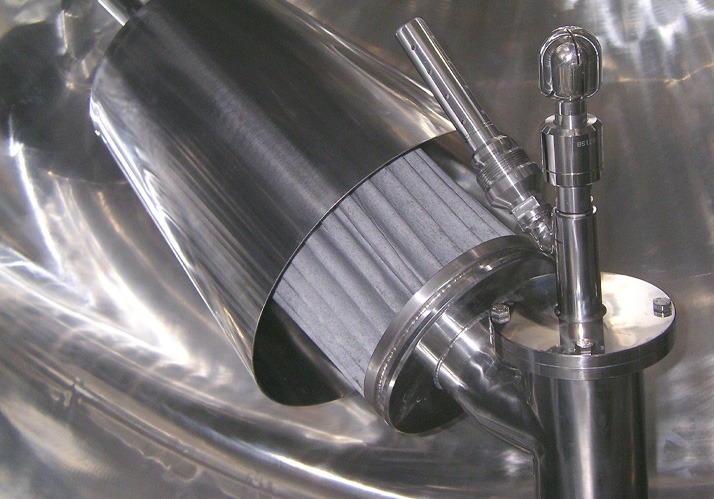
Maximum cleanability
A machine suitable for multiple products must be, above all, easy to clean in order to:
- meet the validation procedures set by FDA Standards;
- avoid product contamination;
- help and speed up changes in product campaigns.
The ease of cleaning of chemical and pharmaceutical industrial systems is usually referred to the following general criteria: internal washing, inspection and dismantling of internal parts, external washing.
Internal washing
Due to the rotation of the drying chamber and the bi-conical internal shape, very few rinses with small quantities of fluid are necessary to achieve the required ppm. values, hence reducing the quantity of wastewater to be disposed of. Furthermore, inside the chamber, a C.I.P. (Clean In Place) device can be applied, able to spray the washing fluid in all directions. Thanks to this fast and complete internal cleaning, Bi-Evolution Dryer® facilitates the easy shift from one product campaign to another.
Inspection and dismantling of internal parts
Inspection and dismantling of internal parts are possible by opening the manhole port lid and the loading hopper. That allows to perform the SWAB test required by the FDA standards for the validation of the washing procedures, with extreme ease and safety. Inside the drying chamber, Bi-Evolution Dryer® presents only the powder filter that can be easily pulled out by means of a special tool.
Clean room installation
Bi-Evolution Dryer® can be easily cleaned both inside and outside. Due to the waterproof casing of the entire machine (cGMP “particle free” configuration), covering insulation, electrical and hydraulic circuits, the external cleaning is extremely easy and effective. This characteristic, combined with the “partitioning” solution, allows the installation in a clean room, allowing the pressurization and separation of the clean room from the technical area.
Turn-key systems
Italvacuum is the only manufacturer in the world that, in addition to the dryer itself, can design and build internally all the auxiliary units to complete the system, properly sizing them to meet every process requirement, vacuum system included:
- High vacuum group Saurus939;
- Vacuum condensation group for reduction of drying time and recovery of extracted solvents;
- Heated external safety cyclone filter, designed to avoid pressure losses and condensation phenomena, for a complete protection of the vacuum line;
- Heating and cooling group for system thermoregulation;
- Control panels with PLC for complete plant management, provided with software that is certifiable according to CFR 21 – Part 11 regulations, and that guarantees reproducibility of the dried batches and communication with centralized supervision systems.
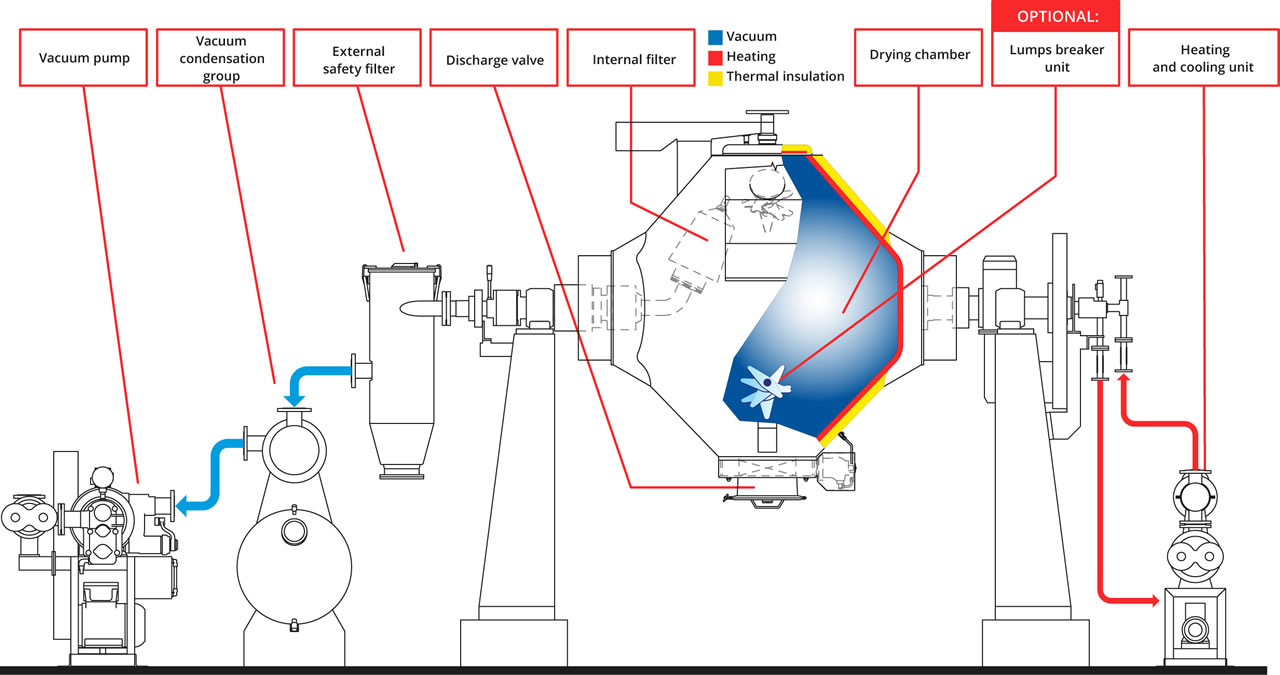
Bi-Evolution Dryer® main features
Dimensions
Bi-Evolution Dryer® can be designed for a wide range of capacities with total volumes ranging from 55 to 12,000 litres. The maximum recommended loading level is a function of the individual product.
![]() |
||||||||||||
Bi-Evolution Dryer® model | 55 | 200 | 350 | 600 | 1000 | 2000 | 3000 | 4000 | 6000 | 8000 | 12000 | |
---|---|---|---|---|---|---|---|---|---|---|---|---|
Totalvolume | (l) | 55 | 200 | 350 | 600 | 1000 | 2000 | 3000 | 4000 | 6000 | 8000 | 12000 |
A | (mm) | 960 | 1330 | 1470 | 1700 | 1980 | 2390 | 2730 | 3000 | 3360 | 3560 | 4070 |
B | (mm) | 2625 | 3075 | 3340 | 3670 | 4060 | 4420 | 4780 | 5190 | 5510 | 6020 | 6430 |
C | (mm) | 1675 | 2095 | 2165 | 2445 | 2695 | 3050 | 3255 | 3440 | 3780 | 3880 | 4135 |
D | (mm) | 805 | 890 | 780 | 830 | 810 | 730 | 635 | 554 | 530 | 380 | 130 |
E | (mm) | 1448 | 1796 | 1900 | 2175 | 2420 | 2770 | 2975 | 3120 | 3490 | 3580 | 3850 |
F | (mm) | 1195 | 1430 | 1430 | 1595 | 1705 | 1855 | 1900 | 1940 | 2100 | 2100 | 2100 |